Heute werde ich mal dämpfen. Aber nicht Deine Erwartungen… und man verzeihe mir dieses misslungene Wortspiel. Es geht natürlich um die Dämpfermechanik. Dabei handelt es sich um die zweitaufwändigste Komponente dieses Projektes und Du kannst Dir denken, welches die Aufwändigste ist, oder?
Als großer Bewunderer von klassischen Flügeln löste die Idee, einen solchen selbst bauen zu können, einen wahren Begeisterungssturm in mir aus. Seit einiger Zeit besitze ich einen echten, akustischen Flügel und träume nicht erst seit dem davon, mich einfach mehr mit dessen Mechanik zu beschäftigen. Aber ich bin halt kein Klavierbauer. Dass dann jemand im Internet ein 3D Druck Modell veröffentlicht hat, das ein sog. Grand Piano originalgetreu und somit voll funktionsfähig abbildet, kam daher wie ein Schicksalsruf.
Erinnere Dich an das Foto mit der Seitenansicht der Repetitionsmechanik. Ganz links darauf siehst Du den Dämpfer. Seine Aufgabe ist es dafür zu sorgen, dass ein Ton nicht ewig nachklingt, sondern beim Loslassen einer Taste auch wieder aufhört zu schwingen. Dazu senkt sich der mit Filz beklebte Dämpferkopf einfach auf den Klangstab. Das mag zwar einfach klingen; aber ein bisschen mehr KnoffHoff steckt da schon drin.
Der Entstehungsprozess
Wie üblich war die Clearance hier ein Thema. Denn in dem Dämpfer steckt ein Metallstab, der wiederum – vereinfacht gesagt – über einen Dämpferlöffel von den Tasten nach oben gehoben wird. Leider passten die Stäbe mit 1,5mm Durchmesser in keinen einzigen Dämpferkopf. Bei der Nachbearbeitung der Löcher war es aber wichtig, sie nicht aus Versehen zu verlängern. Also habe ich improvisiert:
![]() | ![]() | ![]() | ![]() |
![]() | ![]() |
Damit passten die Metallstäbe und ließen sich auch problemlos einsetzen. Im Anschluss kamen die Filz-Teile, die später den Klang dämpfen sollen. Sie mussten auf ungefähr 9×5,5mm zurechtgeschnitten werden. 38 Stück davon. Dazu habe ich mir einen Streifen Filz mit der Breite von ca. 9mm abgeschnitten und mir dann auf der Schneidmatte ein paar “Hilfslinien” vorbereitet:
![]() | ![]() | ![]() |
![]() | ![]() | ![]() | ![]() |
Die nächste Herausforderung bestand darin, die Hebelschiene für die Dämpferköpfe vorzubereiten. Denn die Hebel-Baugruppe (zu der ich gleich noch komme), wird über eine gemeinsame Achse aufgehängt, die dafür durch 38 Ösen geschoben werden muss. Zusätzlich wird die komplette Schiene auch noch über zwei Achs-Stifte im Gehäuse verankert. Die Löcher wollen also alle noch einmal bearbeitet werden. Doch… wer hat schon so einen langen Bohrer?
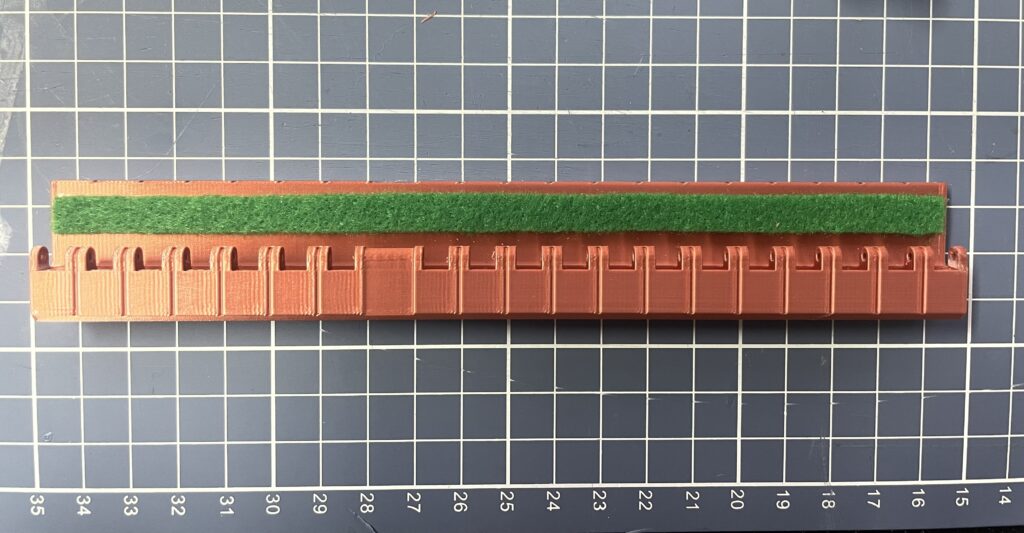
Letztlich habe ich dann einfach eine entsprechend lange Metallstange genommen, sie angespitzt und in meinen Handbohrer eingespannt. Den Tipp gibt es im Assembly Guide leider nicht. Immerhin bin ich von selbst darauf gekommen…
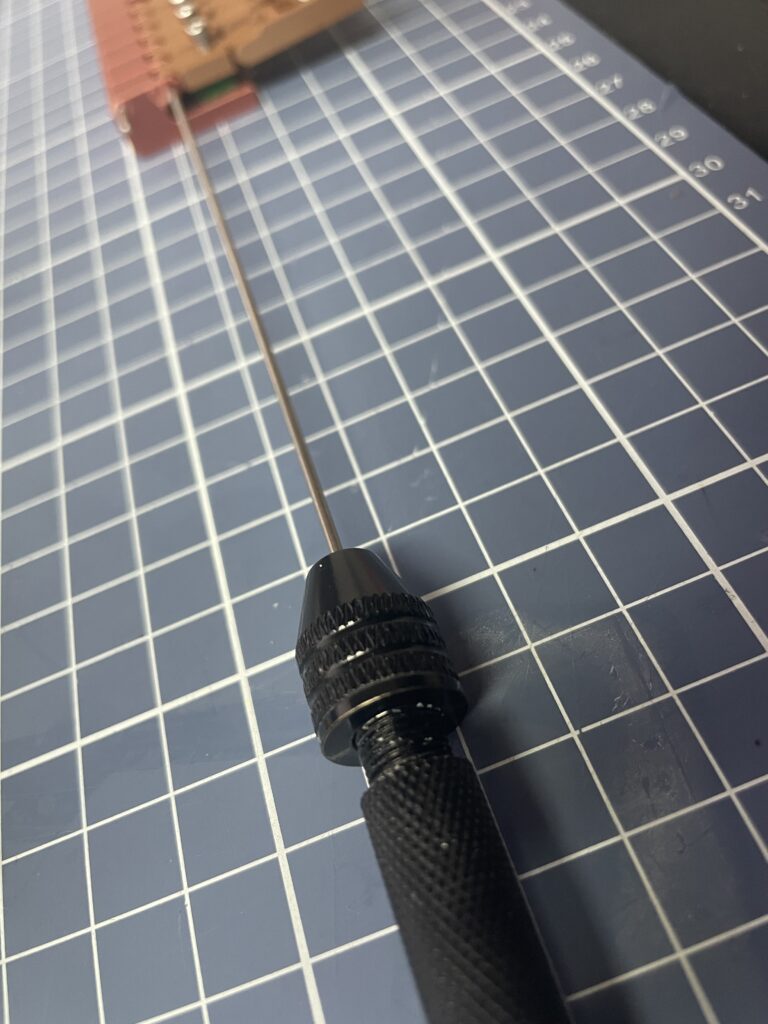
3MF to the rescue
Kommen wir mal zur Hebel-Baugruppe. So präsentiert sich das ganze im Assembly Guide:
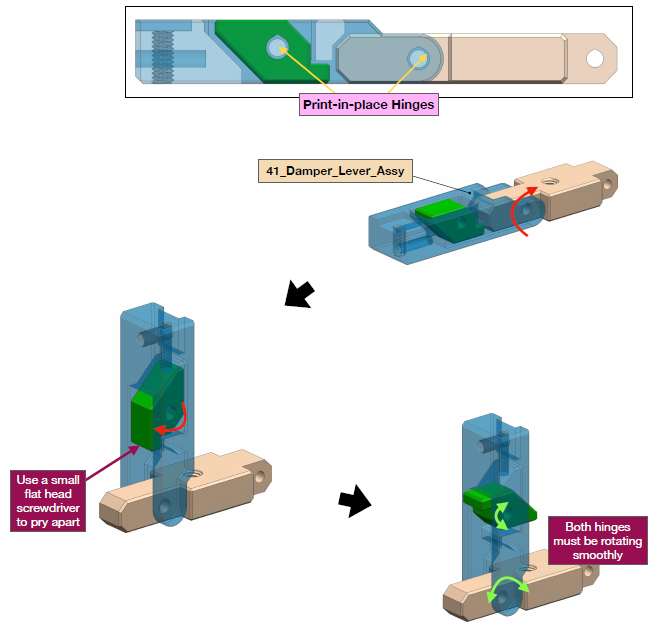
Was da in verschiedenen Farben bunt eingefärbt ist, ist insgesamt genau ein gedrucktes Teil mit zwei integrierten Gelenken. Da das Teil auch noch sehr klein ist, bedeutet das, dass der Drucker sehr exakt arbeiten muss, damit das funktioniert.
Ich will ehrlich sein: Meine ersten Versuche waren nicht brauchbar. Und leider hatte ich zunächst einmal ein Brett vorm Kopf. Lass mich Dir erklären, was passiert ist:
Normalerweise willst Du einen perfekten ersten Layer haben. Dazu gibt es verschiedene Einstellungen, die dabei helfen. Z.B. könntest Du den ersten Layer mit etwas mehr Flow drucken und gleichzeitig etwas daran drehen, dass die Linien sich im Zweifel leicht überlappen. Damit gibt es eine schöne geschlossene Oberfläche, die perfekt auf dem Druckbett haftet.
Tja: Wenn Du nun aber so ein Teil wie dieses hier druckst, kommst Du damit nicht weit. Ich zeige Dir mal die einzelnen Evolutionsschritte meiner Versuche:
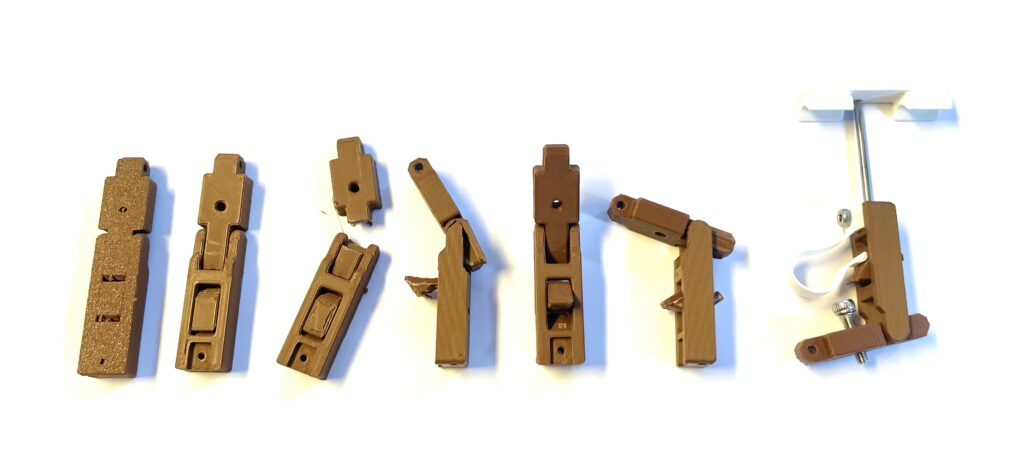
Ganz links auf dem Bild siehst Du die Baugruppe von unten. Sehr schön zu erkennen: Die Oberfläche ist komplett zu. Von oben (zweites Bild) siehst Du gut, wie die einzelnen Teile eigentlich rotieren sollten. Und bei dem Versuch, die Gelenke “freizuknicken”, ist mir so ein Teil doch direkt zerbrochen (Bild 3). In Bild 4 und 5 kannst Du zwar erkennen, die es eigentlich aussehen sollte… so richtig gut bewegte sich da aber immer noch nichts. Laut Assembly Guide sollte sich das vollkommen frei und ohne hängen zu bleiben bewegen lassen können. Wie also bin ich zu Bild 5 gekommen, auf dem Du das komplette Dämpfer-Element einmal testweise zusammengebaut sehen kannst?
Nun, Dan hat mal wieder mitgedacht! Zusätzlich zu den STL-Dateien enthält das Archiv ein Verzeichnis mit .3mf-Dateien. Dabei handelt es sich in diesem Fall um Projektdateien, die mit seinem Drucker entstanden sind. Enthalten sind daher auch alle Slicer-Einstellungen, die er mit Cura gemacht hat… für jedes… einzelne… Teil. Das ganze dient als Referenz, falls man mal auf Probleme stößt.
Also habe ich mein Profil und seines parallel geöffnet, um dann alle Einstellungen abzugleichen. Ich kann Dir sagen: Dabei hatte ich einige Aha!-Momente.
Nach einem Test, ob es nun funktionieren würde (tat es), habe ich dann einfach alle Hebel auf einen Rutsch gedruckt und die kleinen, weißen Federn direkt hinterher:
![]() | ![]() |
Und hier endlich siehst Du alle Dämpfer gemeinsam auf der Schiene:
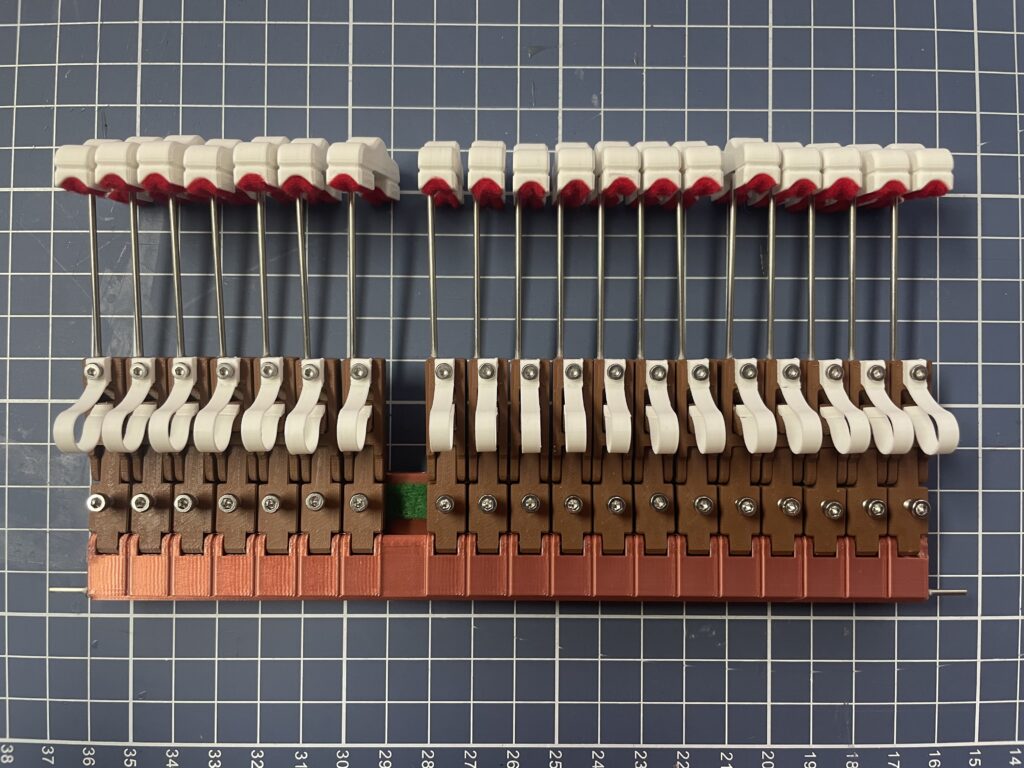
Was für ein Kraftakt! Interessant ist übrigens auch, dass es zum aktuellen Zeitpunkt noch nicht wichtig ist, dass die Dämpferköpfe nicht perfekt auf einer Linie liegen. Denn das wird später beim Regulieren eingestellt.
Hast Du übrigens den kleinen “Nippel” gesehen, der in der Mitte der Hebel-Baugruppe herausragt und von der anderen Seite durch die weiße Feder gehalten wird? Durch ihn entsteht die Magie des Sostenuto-Pedals. Da kommen wir noch zu.
Last but not least noch ein Bild davon, wie die Dämpfermechanik im Flügel-Gehäuse ausschaut:
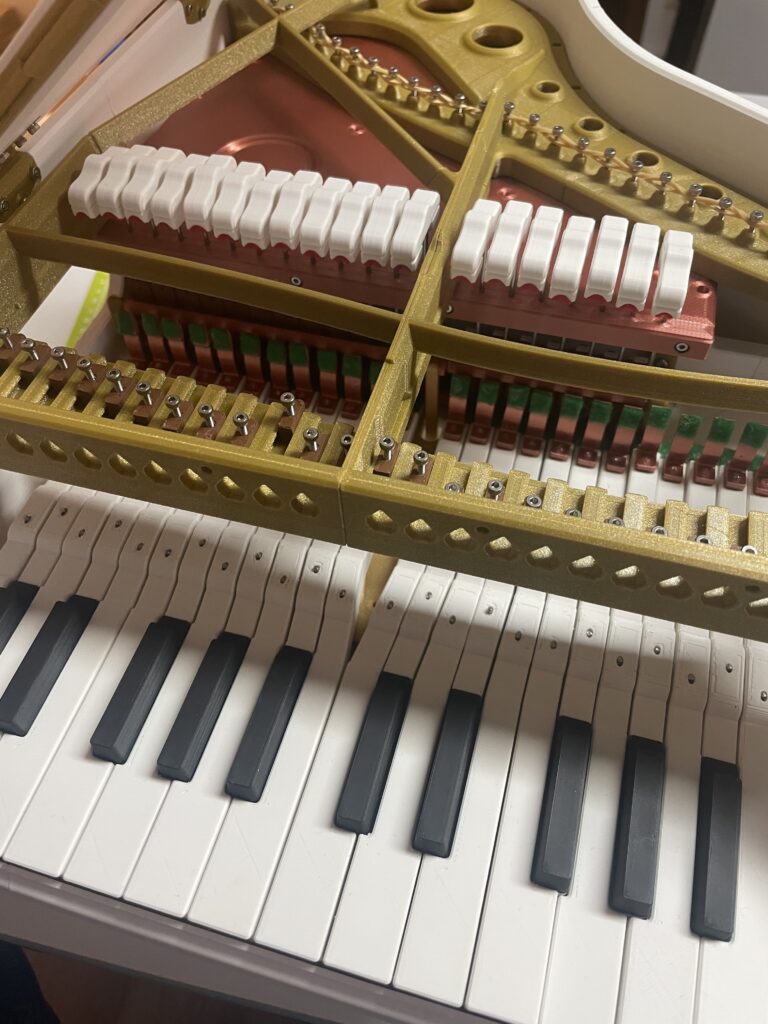
Und ganz nebenbei noch ein Reveal: Der Deckel ist inzwischen auch komplett fertig – inkl. passender Scharniere. Das hatte ich noch gar nicht erwähnt, oder?
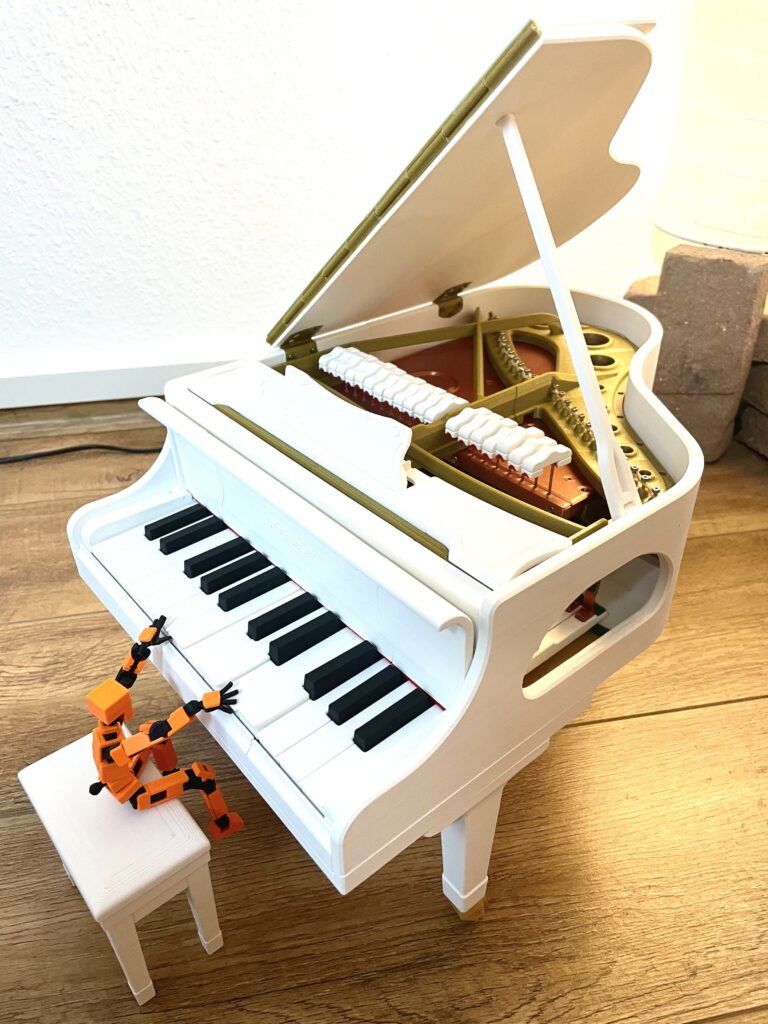
Im nächsten Post fange ich an, von der Hammermechanik zu erzählen. Und dabei handelt es sich dann wirklich um die komplexeste Komponente im ganzen Flügel. Versprochen!
Bis dahin: Hab eine schöne Restwoche!
P.S.: Denk daran: Zum Beispiel alle weißen Elemente hier und auch die schwarzen Tasten bestehen aus extrudr PLA NX2 Filament. Falls Du planst, in nächster Zeit auch direkt bei extrudr.com zu bestellen, benutz doch einfach den Code EX_THINKTWICE und erhalte sofort 20% Rabatt auf Deine Bestellung! |
1 comment on “[3D-Druck] Ich drucke mir einen Flügel – Teil 14”